Fiberglass molding is a specialized process used to form components from fiberglass-reinforced materials. This method leverages the high strength-to-weight ratio of fiberglass to create durable, lightweight, and complex structures. The process is widely used in industries such as automotive, aerospace, marine, and construction.
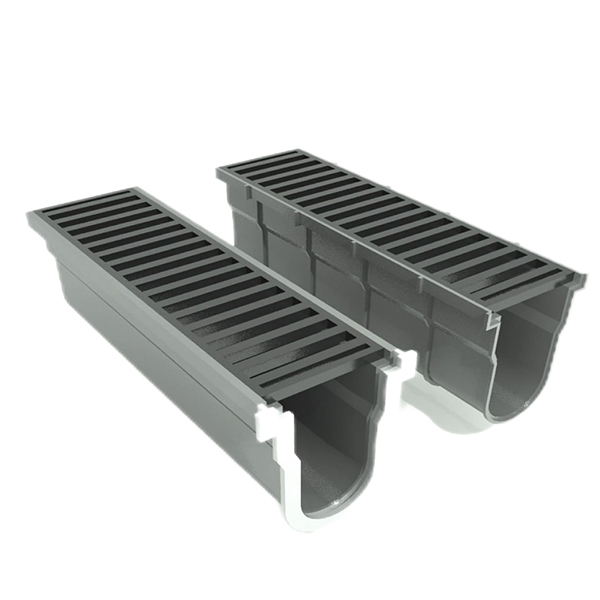
Fiberglass Molded Products
Fiberglass molding involves several steps, from preparing the mold to finishing the final product. Here’s a detailed breakdown of the process:
1. Mold Preparation
Molds are critical in fiberglass molding and can be made from materials like aluminum, steel, or fiberglass itself. Mold preparation involves:
Designing the Mold: The mold must be designed according to the specifications of the final product. The design process includes considerations for parting lines, draft angles, and surface finish.
Cleaning and Polishing: The mold surface needs to be cleaned and polished to ensure a smooth release and high-quality surface finish of the final product.
Applying Release Agent: A release agent (such as wax or silicone-based substances) is applied to the mold to prevent the fiberglass from sticking to it during the curing process.
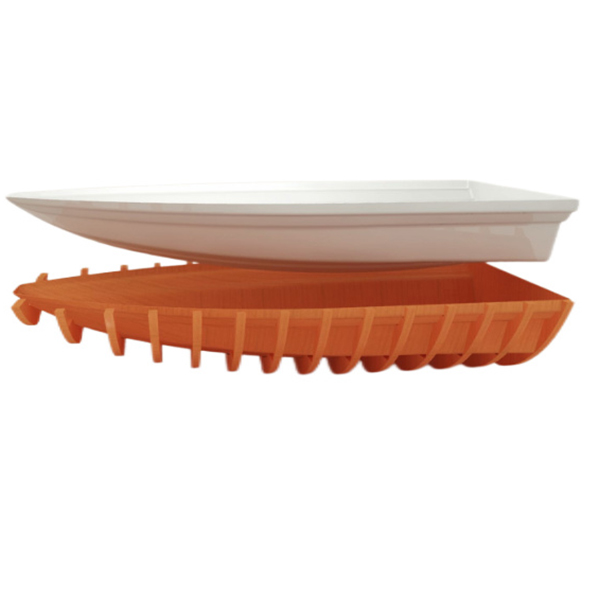
Fiberglass Molded Boat Hull
2. Material Preparation
Fiberglass material is typically prepared in the form of:
● Fiberglass Mats or Fabrics: These are woven or non-woven layers of glass fibers. The type and orientation of the fibers can affect the strength and properties of the final product.
● Resins: Thermosetting resins like polyester, epoxy, or vinyl ester are used. The choice of resin impacts the mechanical properties, resistance to environmental factors, and the overall quality of the final product.
● Catalysts and Hardeners: These chemicals are added to the resin to initiate and control the curing process.
3. Layup Process
● Hand Lay-Up: This is a manual process where fiberglass mats or fabrics are placed into the mold, and resin is applied with brushes or rollers. Each layer is compacted to remove air bubbles and ensure good resin penetration.
● Spray-Up: Fiberglass and resin are sprayed into the mold using specialized equipment. This method is quicker and suitable for larger parts but may not provide as high a precision as hand lay-up.
● Resin Infusion: In this method, dry fiberglass fabric is laid in the mold, and resin is infused under vacuum pressure, ensuring thorough resin distribution and minimal voids.
4. Curing
● Room Temperature Curing: The resin cures at ambient temperature. This method is simple but may take longer and is typically used for small to medium-sized parts.
● Heat Curing: The mold is placed in an oven or autoclave to accelerate the curing process. This method provides better control over the final properties of the product and is used for high-performance applications.
5. Demolding
Once the resin has fully cured, the part is removed from the mold. The demolding process must be handled carefully to avoid damaging the part or the mold.
6. Finishing
● Trimming and Cutting: Excess material is trimmed, and the edges are finished to achieve the desired dimensions and appearance.
● Sanding and Polishing: The surface of the part is sanded and polished to improve the surface finish and aesthetics.
● Painting or Coating: Additional coatings or paints can be applied for enhanced durability, UV protection, or aesthetics.
Types of Fiberglass Molding Processes
Open Mold Processes:
● Hand Lay-Up: Manual application of fiberglass and resin, suitable for low to medium production volumes.
● Spray-Up: Fiberglass and resin are sprayed into an open mold, suitable for larger parts.
Closed Mold Processes:
● Resin Transfer Molding (RTM): Fiberglass is placed in a mold cavity, and resin is injected under pressure. This method produces high-quality parts with excellent surface finish on both sides.
● Vacuum Infusion: Dry fiberglass is placed in the mold, and resin is infused under vacuum. This method is known for producing lightweight and strong parts with minimal voids.
● Compression Molding: Pre-formed fiberglass mats are placed in a mold, and resin is added before the mold is closed and heated to cure the part under pressure.
Applications of Fiberglass Molding
● Automotive: Body panels, bumpers, dashboards, and other components.
● Aerospace: Lightweight structural components, fairings, and interior panels.
● Marine: Hulls, decks, and superstructures of boats and yachts.
● Construction: Roofing, cladding, and structural elements.
● Consumer Goods: Sporting equipment, furniture, and custom parts.
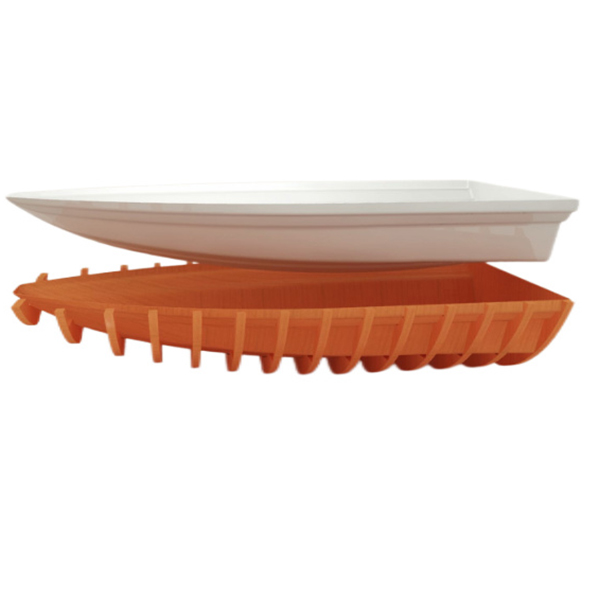
Fiberglass Storage Tank
Advantages and Disadvantages of Fiberglass Molding
Advantages:
● Strength and Durability: Fiberglass parts are strong, lightweight, and resistant to corrosion and impact.
● Complex Shapes: Capable of forming intricate and complex shapes that are difficult to achieve with other materials.
● Customization: Fiberglass parts can be tailored to specific requirements, including varying thicknesses and fiber orientations.
● Cost-Effective: Suitable for both low and high-volume production, offering a balance between performance and cost.
We offer a wide range of raw materials for fiberglass molding processes such as fiberglass roving/fiberglass fabrc/fiberglass mat/resin/cobalt etc.
Our products
Contact us for product information.
Phone number:+8615823184699
Email: marketing@frp-cqdj.com
Website: www.frp-cqdj.com
Post time: Jun-24-2024