Fiberglass rebar, also known as GFRP (Glass Fiber Reinforced Polymer) rebar, is a high-performance alternative to traditional steel reinforcement used in construction. It offers numerous advantages, including corrosion resistance, high strength-to-weight ratio, and electrical non-conductivity, making it particularly suitable for applications in harsh environments and structures requiring long service life. The production process of turning glass fiber roving into fiberglass rebar involves several key steps, from selecting the appropriate glass fiber roving to the final manufacturing of the rebar itself.
The production process begins with the selection of glass fiber roving, which is a collection of continuous glass filaments. The choice of roving is crucial in determining the properties of the final fiberglass rebar. E-glass, which is an alkali-free glass formulation, is commonly used for the production of fiberglass rebar due to its compatibility with polymer matrices and its ability to provide high strength and stiffness. The E-glass roving, with its uniform and continuous filaments, becomes the primary raw material for the manufacturing process.
Once the suitable glass fiber roving is selected, it undergoes a series of processing stages to transform it into fiberglass rebar.
The production process typically involves the following steps:
Roving Preparation: The glass fiber roving is inspected, cleaned, and coated with a sizing material, which improves the adhesion between the glass fibers and the polymer matrix that will later encase the rebar. The sizing also helps protect the glass fibers from abrasion and handling during subsequent processing steps.
Assembly and Formation: Multiple strands of the coated glass fiber roving are assembled and pulled through a resin bath to impregnate them with a polymer resin, typically polyester or vinyl ester. The impregnated rovings are then drawn through a shaping die to form the rebar's desirable diameter and shape.
Curing and Solidification: The formed fiberglass rebar is then subjected to a curing process, where the polymer resin undergoes a chemical reaction to solidify and bond with the glass fibers, resulting in a strong and durable composite material.
Cutting and Packaging: After the curing process, the fiberglass rebar is cut to the desired lengths and packaged for distribution to construction sites and manufacturers for use in concrete reinforcement applications.
The advantages of fiberglass rebar
The advantages of fiberglass rebar over traditional steel reinforcement are numerous and significant. Firstly, fiberglass rebar offers exceptional corrosion resistance, making it ideal for environments where steel rebar would deteriorate over time, such as marine structures, chemical processing facilities, and infrastructure in coastal areas. Its non-conductive properties also make it suitable for use in electrical and MRI-sensitive environments.
Furthermore, fiberglass rebar's high strength-to-weight ratio facilitates easier handling and installation, reducing the labor and time required for construction projects. Its lightweight nature also makes it ideal for applications where reducing overall structural weight is a concern, such as in bridge decks and seismic retrofitting.
In addition to its physical properties, fiberglass rebar provides a long service life with minimal maintenance requirements, contributing to the durability and sustainability of reinforced concrete structures. It also offers design flexibility, allowing for the optimization of reinforcement layouts and the realization of innovative architectural and engineering solutions.
In summary, the production process of converting glass fiber roving into fiberglass rebar involves careful selection and preparation of the raw materials, as well as precise assembly, impregnation, and curing processes. The resulting fiberglass rebar offers several advantages over traditional steel reinforcement, including corrosion resistance, high strength-to-weight ratio, non-conductivity, and long-term durability, making it a compelling alternative for a wide range of construction applications.
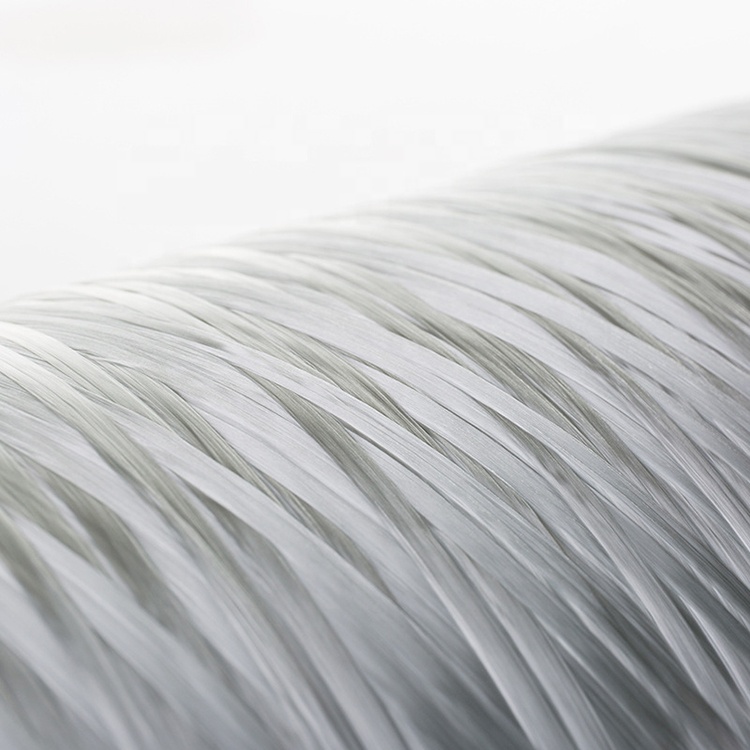
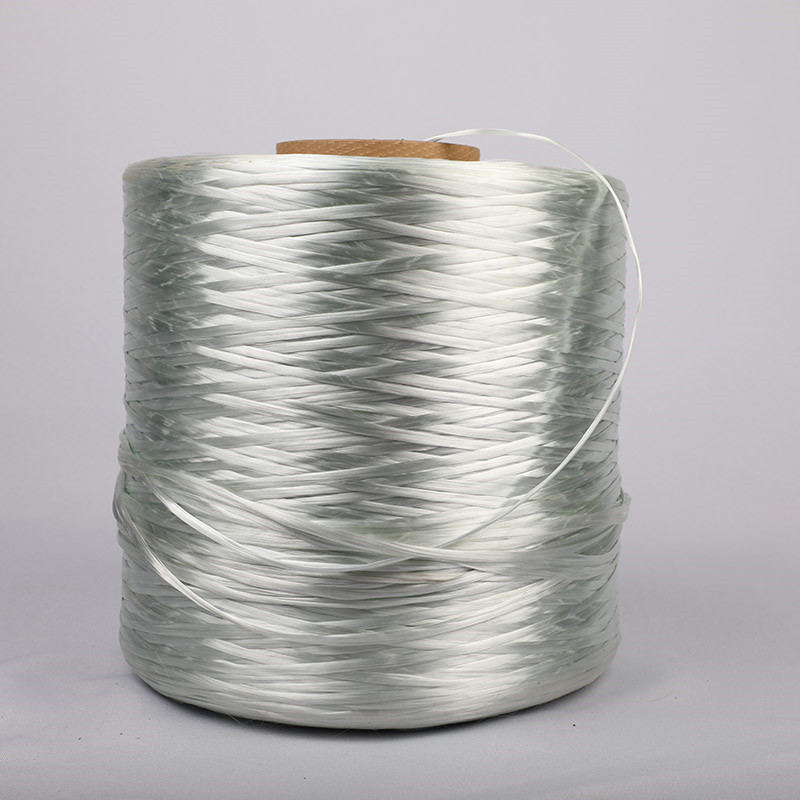
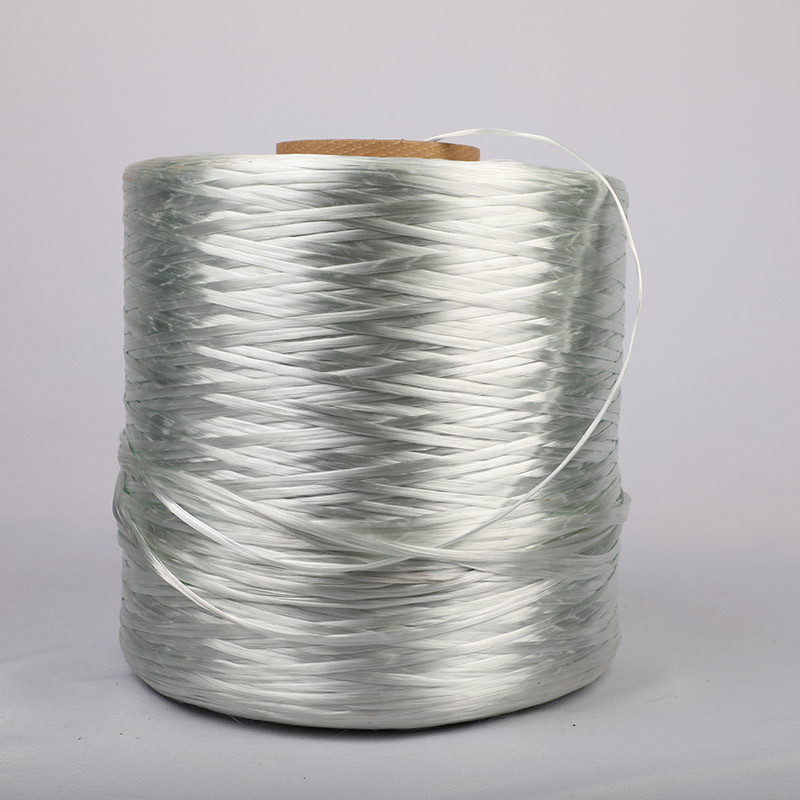
Contact Us:
Phone number/WhatsApp:+8615823184699
Email: marketing@frp-cqdj.com
Website: www.frp-cqdj.com
Post time: Jan-05-2024