To choose the right fiberglass substrate, one must understand its advantages, disadvantages, and suitability. The following outlines general selection criteria. In practice, there is also the issue of resin wettability, so the best approach is to conduct wettability tests at a fiberglass boat manufacturing facility for confirmation.
Secondly, fiberglass mat is mainly used for hand lay-up molding.
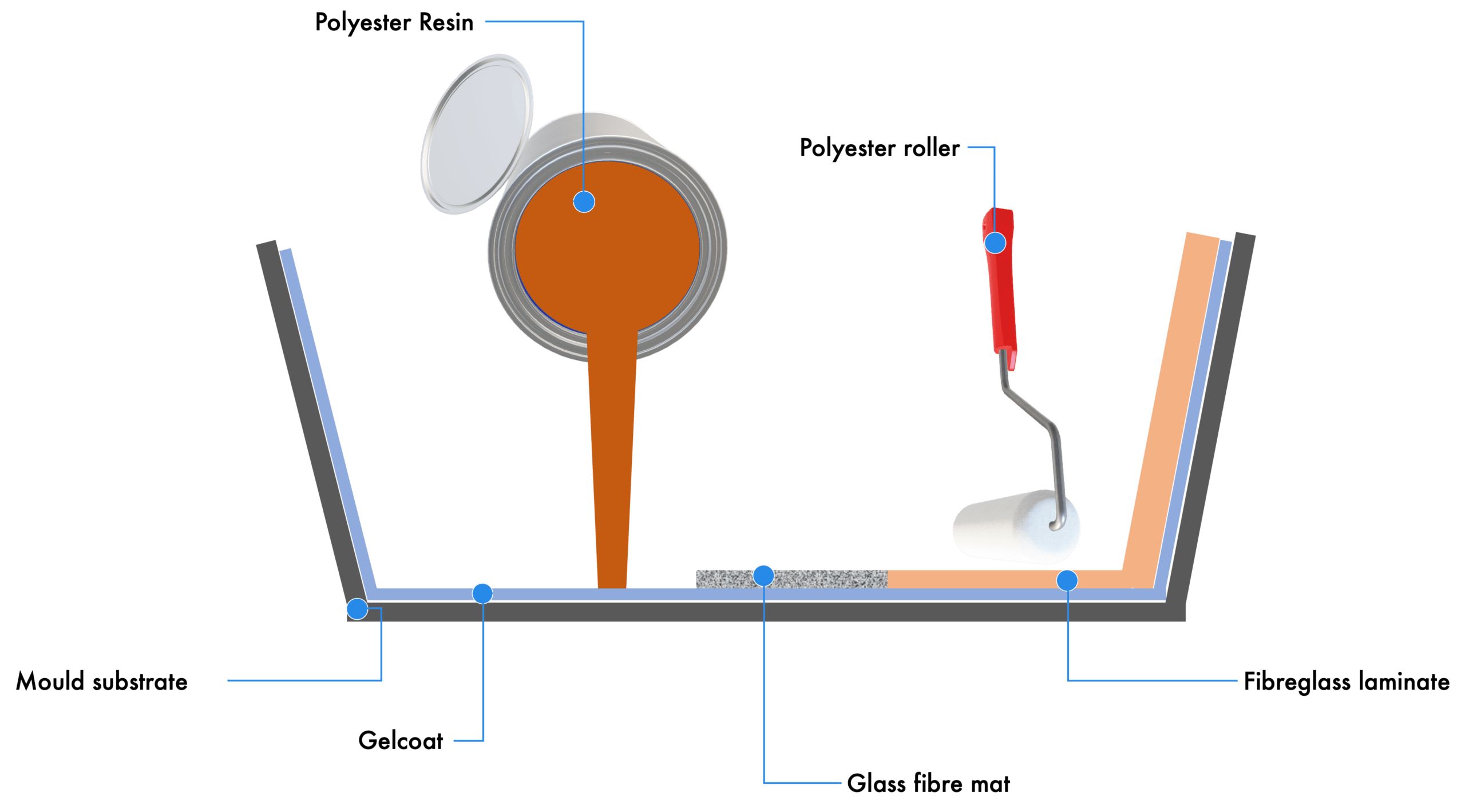
Generally, a good product meets the following conditions:
1.Uniform weight per unit area.
This condition is crucial as it affects both thickness and strength. It is easier to discern under lighting, and severely uneven products can be identified with the naked eye. Uniform thickness is not necessarily ensured by uniform mass per unit area; this directly relates to the consistency of the gap between cold press rollers. Uneven mat thickness leads to uneven resin content in FRP products. If the mat is fluffy, it will absorb more resin. To test the uniformity of mass per unit area, the standard method involves cutting 300mm x 300mm mat samples in the width direction, numbering them sequentially, and weighing them separately to calculate the weight deviation of each sample.
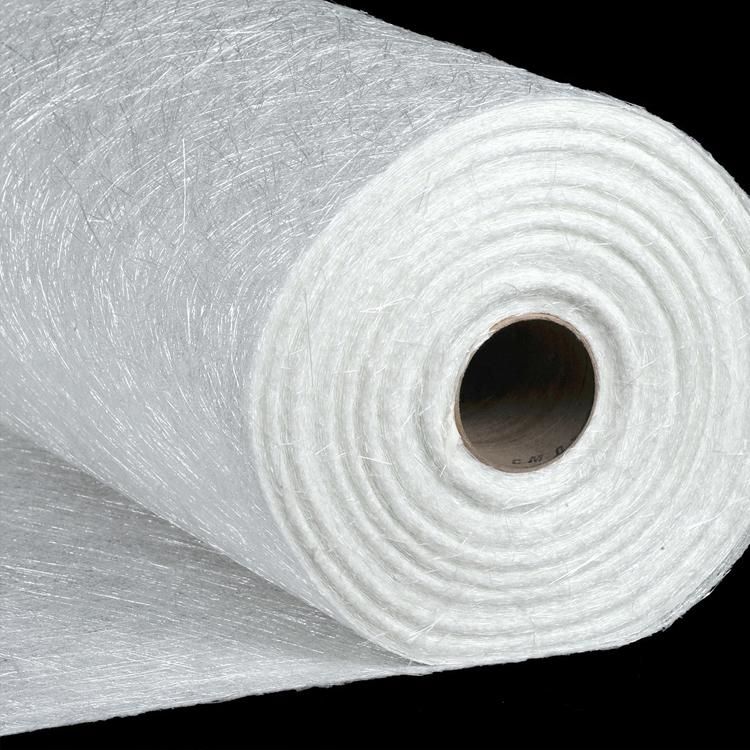
2.Uniform yarn distribution without excessive local accumulation.
The dispersibility of the chopped strands is an important indicator in the production of roving, affecting the uniformity of mat weight per unit area and the distribution state of the strands on the mat. Each bundle of strands should fully disperse after being chopped from the spool (cake). If some strands do not disperse adequately, they can form thick, streaky bundles on the mat.
3.No yarn falling off the surface or delamination.
This relates to the mechanical tensile strength of the mat. Low mechanical tensile strength indicates poor adhesion between the bundles of strands.
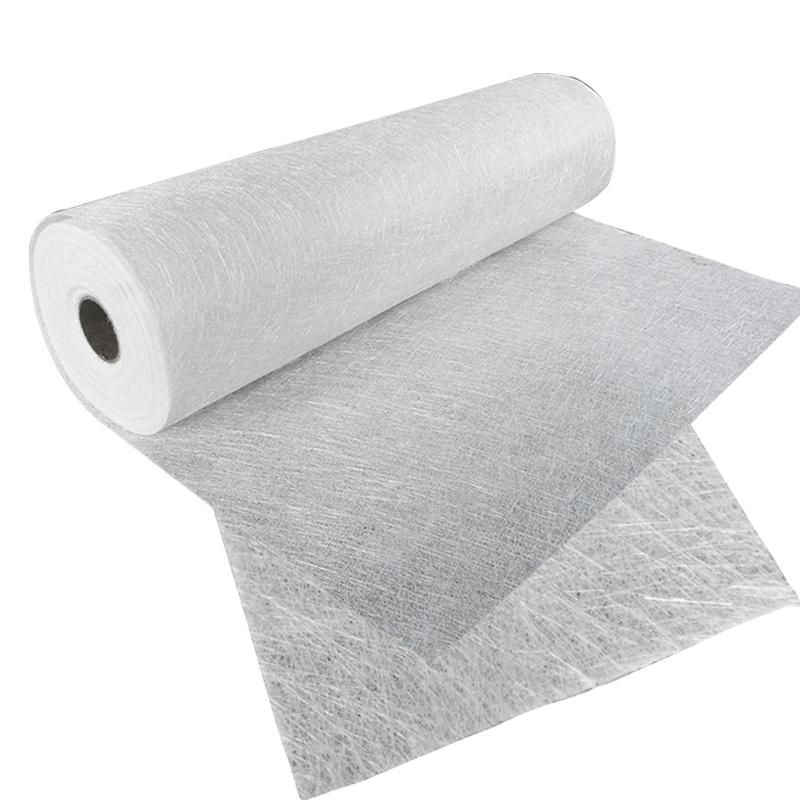
4.No dirt.
Ensuring that the fiberglass chopped strand mat is free of dirt and contaminants is essential for several reasons that impact the quality, performance, and durability of the final composite product.
5.Proper drying.
If the mat is damp, it will fall apart when laid out and picked up again. The moisture content of the mat should be less than 0.2%. For normal production processes, this indicator is generally qualified.
6.Sufficient resin wet-out.
Styrene solubility. Ideally, the mat's solubility in polyester resin should be tested, but this is time-consuming and difficult to quantify. Testing the mat's solubility in styrene instead of polyester resin can indirectly reflect the solubility of fiberglass mat in polyester, and this method is widely accepted and standardized globally.
After the resin has been applied to the fiberglass mat, it is crucial that the yarns do not relax or shift.
7.No yarn relaxation after resin wet-out.
8.Easy deaeration.
At CQDJ, we specialize in manufacturing high-quality fiberglass chopped strand mats, designed to meet the rigorous demands of various industrial applications. Our mats are crafted with precision and care, ensuring superior performance, durability, and reliability. Here’s what sets our fiberglass chopped strand mats apart:
1.Uniform Weight Per Unit Area:
Our mats are produced with meticulous attention to maintaining a uniform weight per unit area. This ensures consistent thickness and strength across the entire mat, providing reliable performance in all applications.
2.Excellent Resin Wettability:
Our fiberglass mats exhibit outstanding resin wettability, allowing for thorough impregnation with various resins. This ensures strong adhesion between the fibers and the resin, resulting in composites with superior mechanical properties.
3.Superior Fiber Distribution:
We ensure that the chopped strands are evenly distributed throughout the mat, preventing local accumulations and ensuring uniform strength and structural integrity.
4.High Mechanical Strength:
Our mats are designed to deliver excellent mechanical tensile strength, ensuring that the fibers remain well-bonded and stable during resin application and throughout the life of the composite product.
5.Clean and Contaminant-Free:
Cleanliness is a top priority in our manufacturing process. Our mats are free from dirt and contaminants, ensuring optimal resin flow and adhesion, as well as a high-quality surface finish for the final composite product.
6.Optimal Drying and Moisture Control:
We ensure that our mats are properly dried, with a moisture content of less than 0.2%. This prevents issues related to dampness, such as mat disintegration during handling and uneven resin absorption.
7.Ease of Handling and Application:
Our fiberglass chopped strand mats are designed for ease of handling, cutting, and lay-up, making them ideal for hand lay-up molding and other composite manufacturing processes.
8.Global Standards Compliance:
Our products comply with international standards for fiberglass materials, ensuring that they meet the quality and performance requirements of customers worldwide.
Applications:
Our fiberglass chopped strand mats are versatile and can be used in a wide range of applications, including:
1.Marine:
Boat hulls, decks, and other marine structures where durability and resistance to water and corrosion are essential.
2.Automotive:
Body panels, interior components, and structural parts that require lightweight yet strong materials.
3.Construction:
Roofing, wall panels, and structural reinforcements that benefit from the strength and stability of fiberglass composites.
4.Industrial:
Pipes, tanks, and other industrial components that need to withstand harsh chemical environments and mechanical stress.
5.Consumer Goods:
Sporting goods, recreational products, and other items that require high-performance composite materials.
Our Mat:
Contact Us:
Phone number:+8615823184699
Email: marketing@frp-cqdj.com
Website: www.frp-cqdj.com
Post time: May-30-2024