Industrial Applications
Fiberglass grating is exceptionally resistant to a wide range of corrosive substances, including acids, alkalis, and various other chemicals. This resistance is largely attributed to the composite structure of the grating, which is made up of high-strength glass fibers embedded in a resilient resin matrix. The choice of resin plays a crucial role in determining the grating's chemical resistance properties. For instance, vinyl ester resin offers superior resistance to acidic environments, while polyester resin is commonly used for general chemical resistance.
1. Resistance to Acids
Fiberglass grating is highly effective in environments where acidic substances, such as sulfuric acid, hydrochloric acid, or nitric acid, are prevalent. These acids can cause severe corrosion in traditional materials like metal, leading to rapid deterioration and failure. Fiberglass grating, on the other hand, remains unaffected, maintaining its structural integrity and performance.
Example: In a chemical processing plant, fiberglass grating is used for walkways and platforms that come into contact with acid spills or vapors.
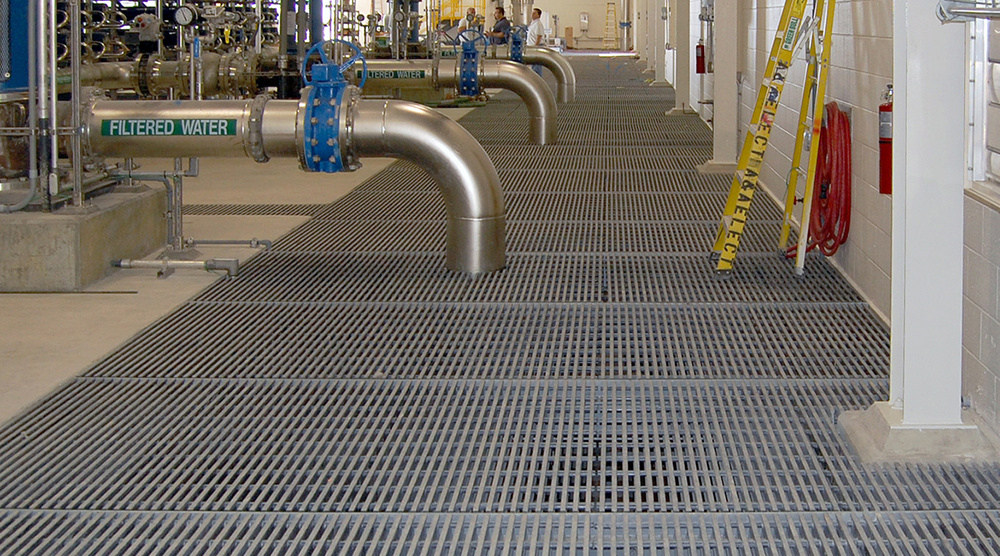
2. Resistance to Alkalis
In addition to acids, fiberglass grating is also resistant to alkalis such as sodium hydroxide and potassium hydroxide. Alkalis are often used in industrial processes and can cause significant corrosion to metals and other materials. Fiberglass grating’s resilience to these substances makes it a preferred choice in industries such as food and beverage processing, pulp and paper manufacturing, and power generation, where alkaline substances are frequently encountered.
Example: In a food processing plant, fiberglass grating is used in areas where cleaning agents containing alkalis are regularly applied. Its resistance to these chemicals ensures that the grating remains intact and functional, providing a safe and hygienic working surface.
3. Customizable to Specific Needs
Fiberglass grating can be customized to meet specific chemical resistance requirements by selecting appropriate resins and adding protective coatings. This allows it to be tailored for specialized applications where certain chemicals are prevalent, ensuring optimal performance and longevity.
Example: In a custom installation at a pharmaceutical manufacturing facility, fiberglass grating is selected with a special resin that provides enhanced resistance to a specific solvent used in the production process. This customization ensures that the grating withstands the unique chemical environment of the facility.
Marine and Offshore Applications
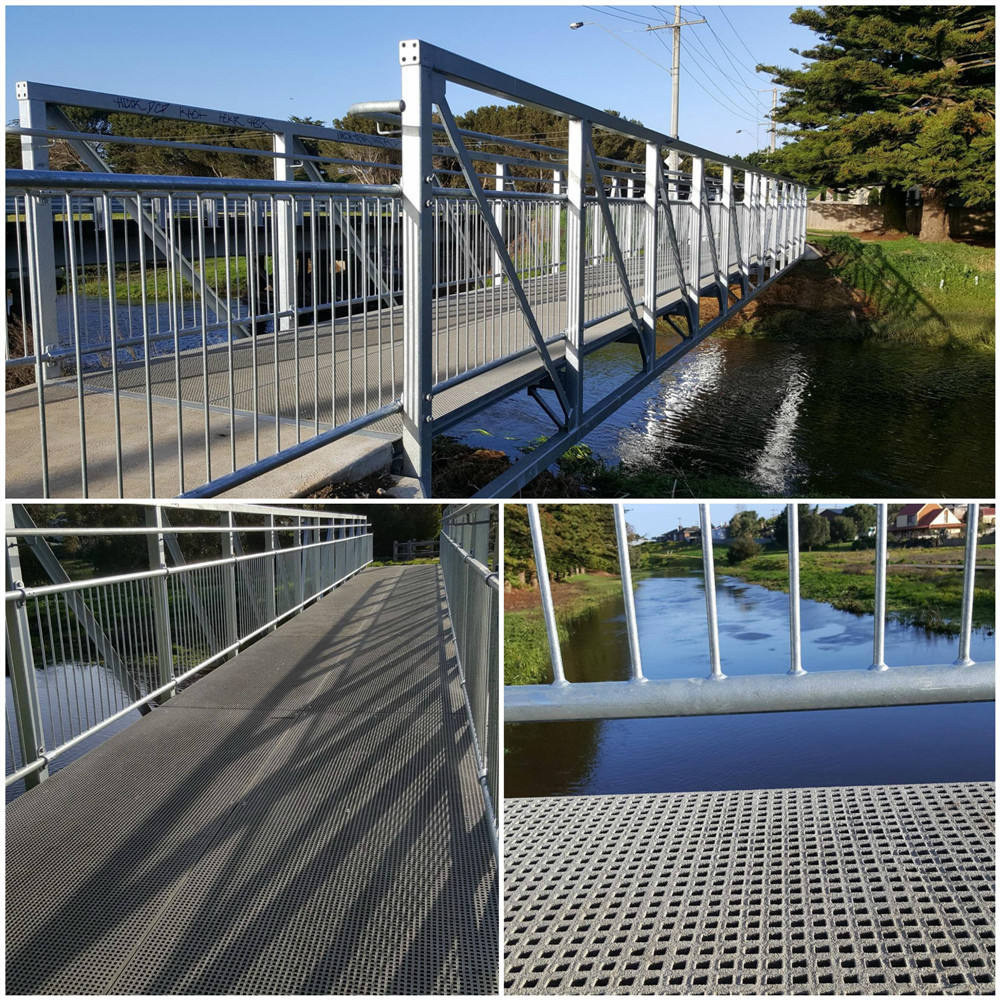
Marine Applications
1. Shipbuilding
Applications
Decking: Provides a durable and non-slip surface for ship decks.
Walkways: Used on cargo ships, ferries, and other vessels to ensure safe passage for crew and passengers.
Stair Treads: Ensures non-slip surfaces on ship stairways, improving safety in wet conditions.
Hatches and Covers: Used for access covers on deck, providing corrosion-resistant closures for equipment and storage areas.
2. Marinas and Docking Facilities
Applications
Floating Docks: Used as a non-corrosive and lightweight surface for floating dock systems.
Walkways and Piers: Provides a safe and durable surface for access areas and piers.
Boat Ramps: Used in boat launch areas to provide a slip-resistant surface.
Gangways: Ensures safe passage between docks and boats.
Commercial and Architectural Applications
1. Public Walkways and Bridges
Usage: Walkway surfaces and bridge decking.
Advantages: Provides a durable, non-slip surface that is lightweight and requires minimal maintenance.
2. Building Facades
Usage: Decorative panels and sunshades.
Advantages: Offers aesthetic flexibility with different colors and designs, along with durability against weathering.
3. Parks and Recreation Areas
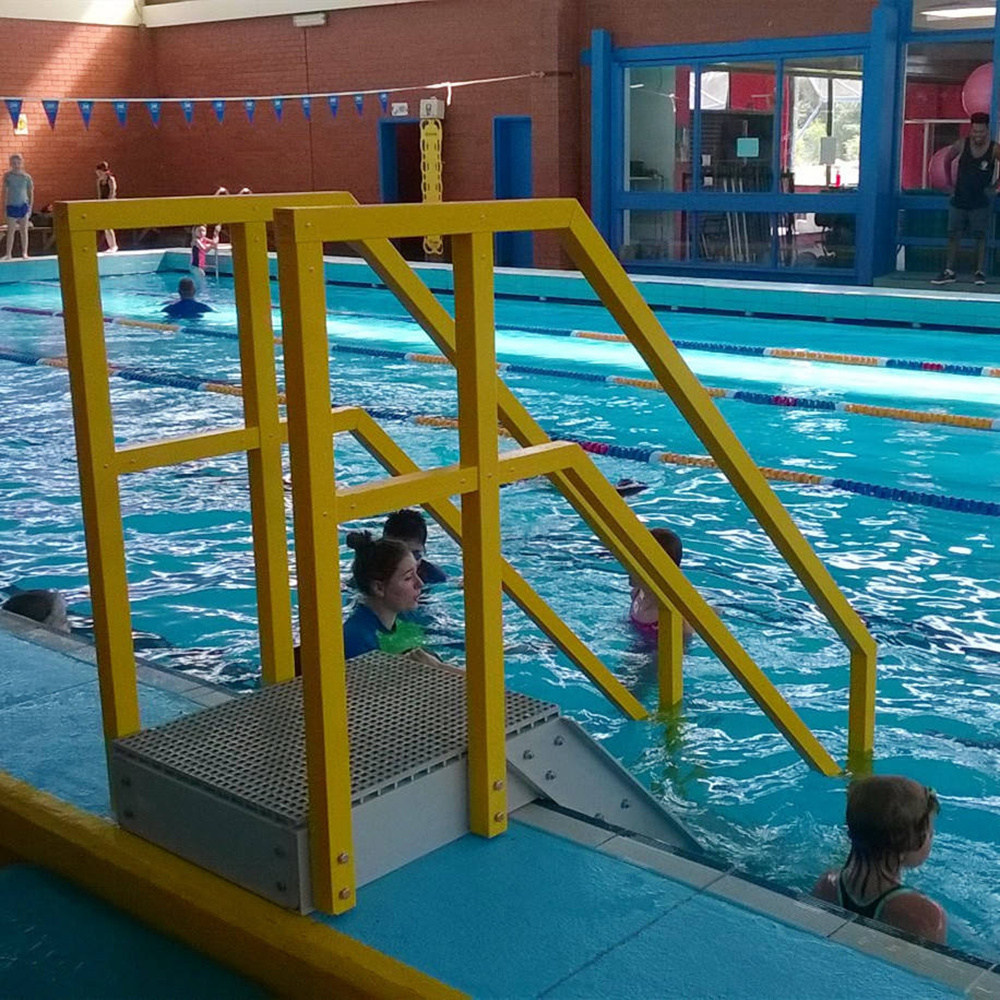
Usage: Boardwalks, playground surfaces, and observation decks.
Advantages: Non-slip, weather-resistant, and available in various colors and textures for safe and appealing public spaces.
4. Parking Structures
Usage: Flooring, drainage covers, and stair treads.
Advantages: Resistant to corrosion from de-icing salts and chemicals, providing a long-lasting solution for exposed areas.
The advantages of choosing FRP grating can be summarized as follows:
FRP grating is a material with a high strength-to-weight ratio. Compared to steel, it is lighter in weight but has comparable strength. This makes it an ideal choice for areas where high strength is required but weight is limited. For example, FRP grating can be used as walkways, platforms, and stair treads.
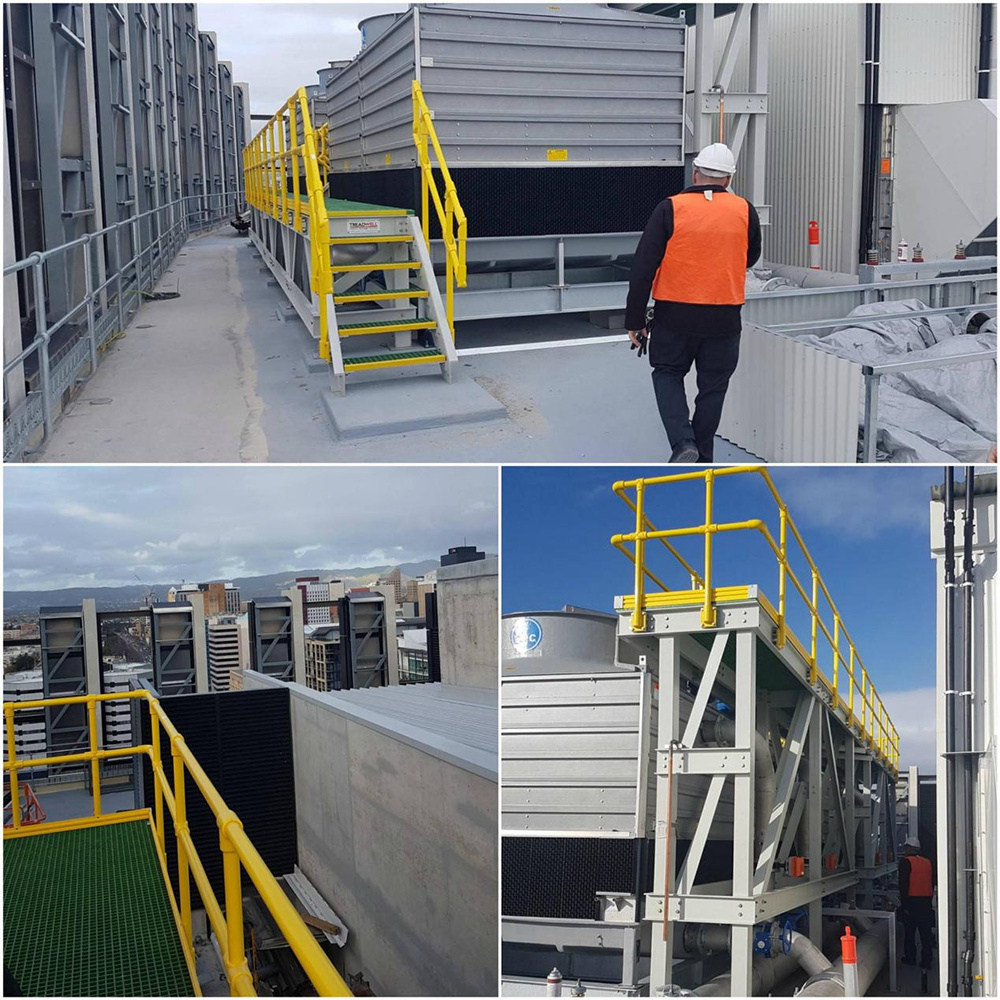
In addition to its high strength-to-weight ratio, FRP grating is also durable and corrosion-resistant. It is not affected by a variety of chemicals, including salt water, which makes it a good choice for coastal areas and industrial environments that require the use of corrosive chemicals. FRP grating also does not require as frequent maintenance as steel, saving time and money.
Finally, FRP grating is a cost-effective material, especially considering its lifespan. While its initial cost may be higher than steel, its durability and low maintenance requirements mean that it costs less in the long run.
Overall, FRP grating is a versatile, durable, and cost-effective material that is a good choice for many applications.
Contact Us:
Phone number/WhatsApp:+8615823184699
Email: marketing@frp-cqdj.com
Website: www.frp-cqdj.com
Post time: Jul-13-2024