Release agent is a functional substance that acts as an interface between a mold and the finished product. Release agents are chemically resistant and do not dissolve when in contact with different resin chemical components (particularly styrene and amines). They also possess heat and stress resistance, making them less likely to decompose or wear out. Release agents adhere to the mold without transferring to the processed parts, ensuring they do not interfere with painting or other secondary processing operations. With the rapid development of processes such as injection molding, extrusion, calendering, compression molding, and laminating, the usage of release agents has significantly increased. In simple terms, a release agent is an interface coating applied to the surfaces of two objects that tend to stick together. It allows the surfaces to separate easily, remain smooth, and stay clean.
Applications of Release Agents
Release agents are widely used in various molding operations, including metal die-casting, polyurethane foam and elastomers, fiberglass-reinforced plastics, injection-molded thermoplastics, vacuum-formed sheets, and extruded profiles. In molding, other plastic additives like plasticizers sometimes migrate to the interface. In such cases, a surface release agent is needed to remove them.
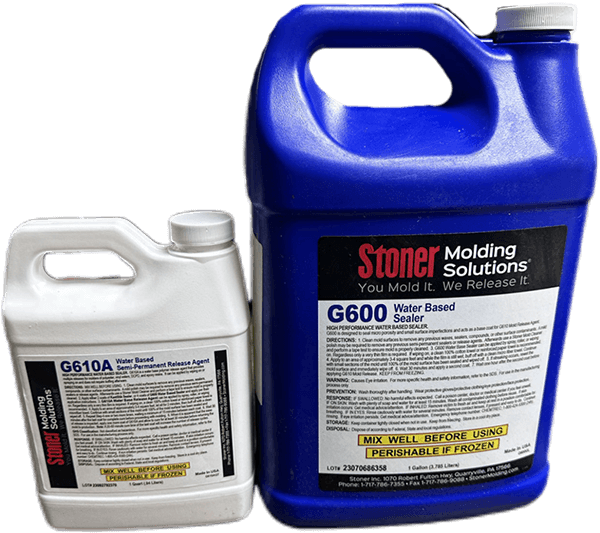
Classification of Release Agents
By usage:
Internal release agents
External release agents
By durability:
Conventional release agents
Semi-permanent release agents
By form:
Solvent-based release agents
Water-based release agents
Solvent-free release agents
Powder release agents
Paste release agents
By active substance:
① Silicone series – mainly siloxane compounds, silicone oil, silicone resin methyl branched silicone oil, methyl silicone oil, emulsified methyl silicone oil, hydrogen-containing methyl silicone oil, silicone grease, silicone resin, silicone rubber, silicone rubber toluene solution
② Wax series – plant, animal, synthetic paraffin; microcrystalline paraffin; polyethylene wax, etc.
③ Fluorine series – best isolation performance, minimal mold contamination, but high cost: polytetrafluoroethylene; fluororesin powder; fluororesin coatings, etc.
④ Surfactant series – metal soap (anionic), EO, PO derivatives (nonionic)
⑤ Inorganic powder series – talc, mica, kaolin, white clay, etc.
⑥ Polyether series – polyether and fatty oil mixtures, good heat and chemical resistance, mainly used in certain rubber industries with silicone oil restrictions. Higher cost compared to silicone oil series.
Performance Requirements for Release Agents
The function of a release agent is to smoothly separate the cured, molded product from the mold, resulting in a smooth and even surface on the product and ensuring the mold can be used multiple times. The specific performance requirements are as follows:
Release Property (Lubricity):
The release agent should form a uniform thin film and ensure that even complex-shaped molded items have precise dimensions.
Good Release Durability:
The release agent should maintain its effectiveness over multiple uses without needing frequent reapplication.
Smooth and Aesthetic Surface:
The molded product's surface should be smooth and aesthetically pleasing, without attracting dust due to the stickiness of the release agent.
Excellent Post-Processing Compatibility:
When the release agent transfers to the molded product, it should not negatively affect subsequent processes such as electroplating, hot stamping, printing, coating, or bonding.
Ease of Application:
The release agent should be easy to apply evenly across the mold surface.
Heat Resistance:
The release agent should withstand the high temperatures involved in the molding process without degrading.
Stain Resistance:
The release agent should prevent contamination or staining of the molded product.
Good Moldability and High Production Efficiency:
The release agent should facilitate the molding process and contribute to high production efficiency.
Good Stability:
When used with other additives and materials, the release agent should maintain stable physical and chemical properties.
Non-Flammability, Low Odor, and Low Toxicity:
The release agent should be non-flammable, emit low odors, and be low in toxicity to ensure safety and comfort for workers.
Contact us for Release Agent.
Phone number:+8615823184699
Email: marketing@frp-cqdj.com
Website: www.frp-cqdj.com
Post time: Jun-07-2024